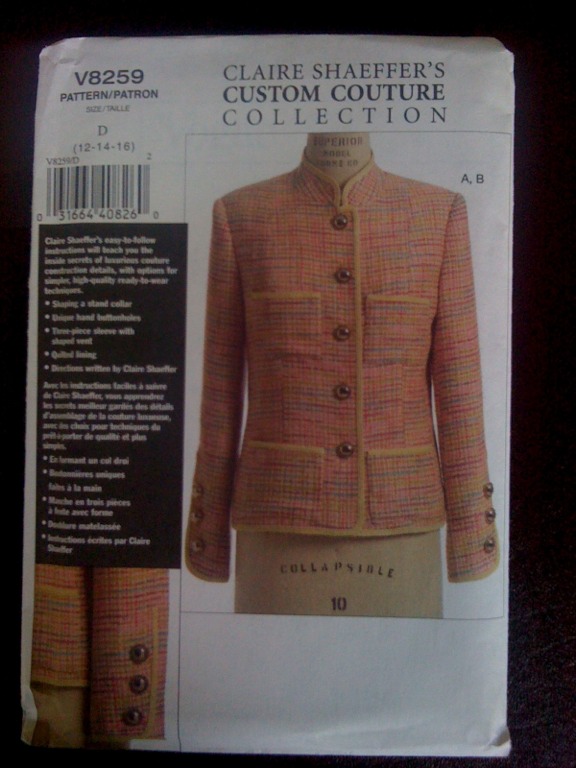
I am pretty sure I want to use a 3 piece sleeve for my Chanel jacket, but the problem is I have a custom drafted two piece sleeve and I am not sure how to convert it to three pieces. I searched my pattern stash, and it turns out, I have Vogue 8529 which has a three piece sleeve. I examined the pieces, and the three seam lines appear to go along the outer arm and about an inch to either side of the underarm. Perfect. Now, I just have to make my two piece draft into a three piece draft.
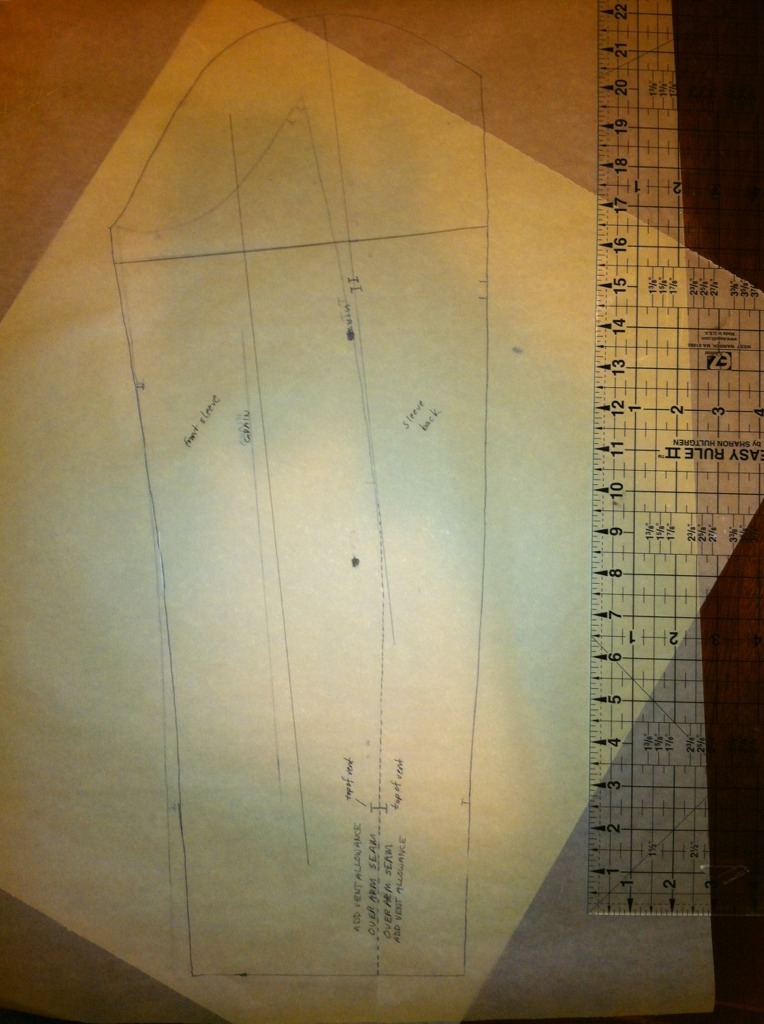
Here is what I did last night. I started with my Bernina My Label jacket sleeve which is a two piece sleeve. I traced it without seam allowances onto tracing paper and marked the grain line. Next, I marked a line perpendicular to the grain line on each piece a little below the curved section at the top of the pieces. I laid the overarm piece on top of the underarm piece wrong sides together and used the angle to help me add a seam line down the outside of the arm.
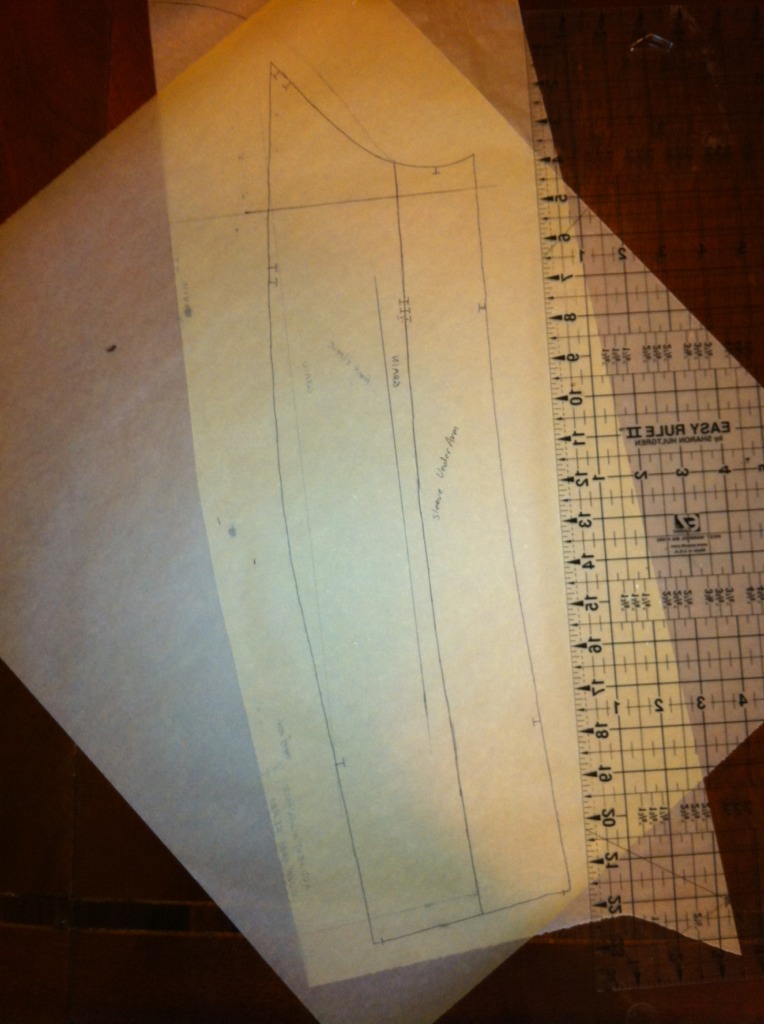
Next, I split the underarm piece so that my new underarm piece is only two inches wide - the same width I will use for my side panels when I alter the jacket side-front and side-back pieces. This left me with four pieces. The next step is to combine the overarm back piece with the underarm back piece.
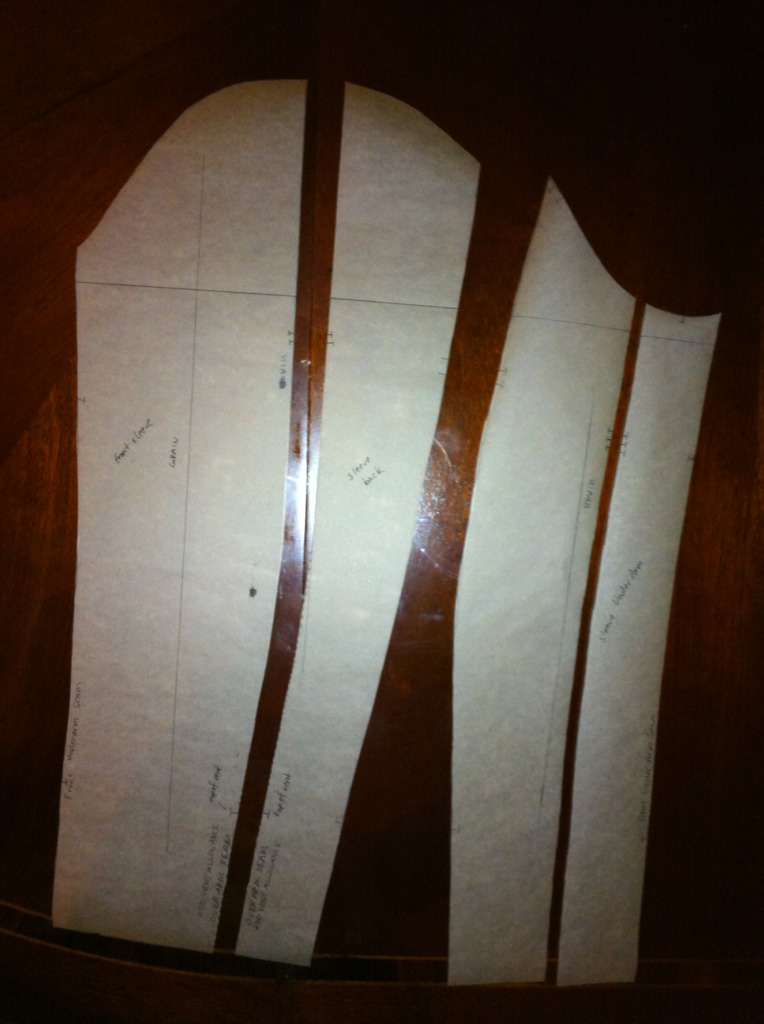
This is where I got stuck. How do I combine the middle two pieces? What happens to the sleeve dart? I am thinking it converts to ease at the underarm seam and the top of the sleeve where it is set in. I think I am going to cut that third piece at the perpendicular line and flip the bottom portion from left to right so that the dart leg becomes the underarm seam when I merge the pieces together.
I think that looks right. I will make a sample and report my results. In the meantime, my daughter has asked me to make her a pair of jeans. I am trying to decide whether to go with the Jalie 2908 pattern that everyone loves so much, or use Bernina My Label. She's 17 with no figure problems. Any advice?